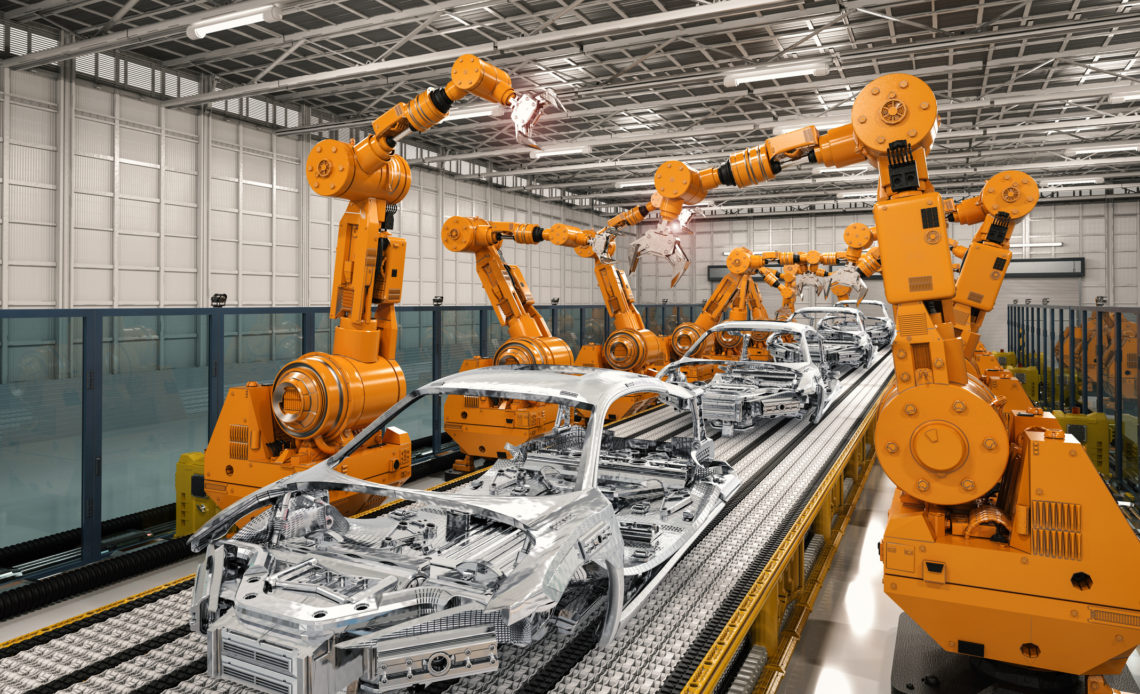
System innovation and integration are the lynchpins of customization at scale in the automotive manufacturing industry. The time lags between design, product development, manufacturing execution, and shopfloor management, and their costs have bedeviled customization, which is reserved for the upper end of the automotive market. Today, every Joe craves vehicles catering to their fancies. Flexible automation is the first step in having it both ways—enjoying luxury products and keeping prices close to standard products.
Making mass customization economically feasible with IoT and AI
The next step in the holy grail to mass customization is an automated product life cycle aided by artificial intelligence. The design, product development, and manufacturing must be synchronized to function with clockwork efficiency with automation to minimize time lags. CAD/CAM began the process of digitization of all processes in the automotive industry. By contrast, shopfloor processes have been slow to keep pace with CAD/CAM. This is because data from the shopfloor flows from physical machines to software-based systems and applications that use very different protocols and metadata or the methods to exchange, classify and organize data.
The Internet of Things has paved the way for data capture from every nook and corner of manufacturing facilities. The data is essential for the automotive industry to adapt to a manufacturing environment where routing, scheduling, load balancing, and performance management changes as new product models favor the marketplace.
However, the raw data is not valuable until it can be analyzed on the cloud or its extension at the edge or the MEC. The data travels from south to north or from physical systems to analytical applications and needs a common language for its transportation before being analyzed. The barriers to the flow of the detailed data for all processes are beginning to break.
The importance of private cellular (4G or 5G) networks is growing exponentially as the data volumes in automotive plants catapult. Process optimization needs granular data such as acoustic emission data from the sensors embedded in CNC machines to determine wear and tear and the risk of tool breakage. It takes machine learning to correlate the acoustic data with physical realities. Increasing the use of lightweight materials and new processes such as joining and adhesive joining aggravate matters. Furthermore, the private cellular networks create the environment for secure remote control of manufacturing processes.
Foundations of Industry 4.0
Operating technologies on shopfloors use proprietary technologies with hardware and software intertwined. Typically, data sources are shop floor machines, Supervisory Control and Data Acquisition-Systems (SCADA), Manufacturing Execution System (MES), Enterprise Resource Planning (ERP) systems, Distributed Control System (DCS) systems besides external supplier data. This data needs to be aggregated to use for machine learning and artificial intelligence to optimize, monitor, and control industrial processes and to do so in a secure manner. Industry 4.0 is building open platforms for aggregating data for telemetry, control, and device management. The data is critically important in the Industry 4.0 context, where the continuity of operations requires a continuous flow of data.
Automobile companies have shifted to standardized data since 2020. VW, for example, announced a shift to standardized data that can be integrated with the cloud. It began with fixed and wireless connectivity but left the door open for 5G connectivity.
Reducing downtime costs and vehicle recalls is the urgent need to use data and analytics to monitor and control processes and preempt losses from unnoticed flows in production processes. The cost of downtime is estimated to be $22,000 per minute. Costs of vehicle recall are in the billions.
Private 5G networks and Industry 4.0
The automotive industry, in the era of Industry 4.0, seeks private wireless networks that afford complete control over its internal processes. Germany’s automotive sector has led in private 5G network deployments, including notably Bosch in collaboration with Nokia. Audi, BMW, Daimler, Mercedes Benz, and Porsche are other top-tier companies investing in private 5G networks. Porsche, in collaboration with Ericsson with its Intelligent Automation Platform using a 5G Standalone network, has deployed a private network for massive amounts of data between machines, production workers, and vehicles for real-time transmission and remote control of robots.
Ford Motor Company has collaborated with Vodafone to deploy a 5G network that uses sensor-generated data from its electric vehicle plant in Essex. The motor and battery of an electric car require a thousand welds generating 500,000 pieces of data. The data is represented on a digital twin and shared with experts for remote assistance in removing inefficiencies in current processes.
Conclusion
The success of automotive 4.0 hinges on pervasive data gathering with sensors and its analysis at the edge and the cloud for unforgiving quality control. The cost of human error is enormous and can bankrupt a company. Digital transformation in the automotive industry is reaching a point where software processes touch every activity in the industry. The data from virtualized processes will bring the intelligence to achieve today’s quality standards.