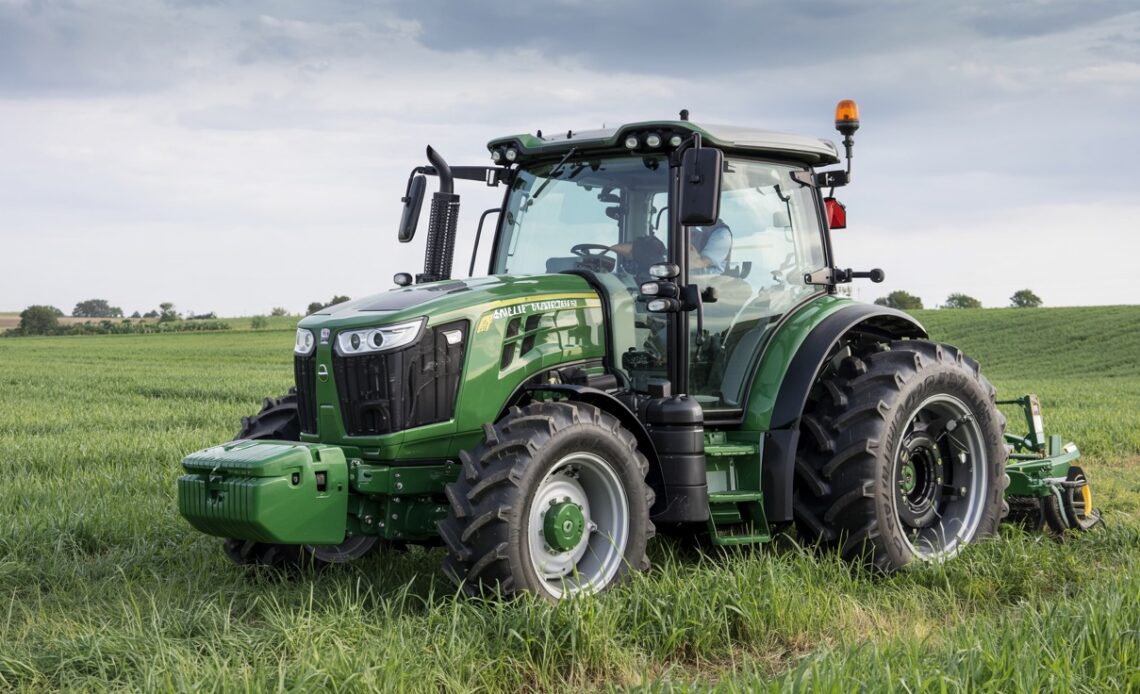
Vertical: Manufacturing
Application: IoT connectivity, smart tools, inventory tracking, digital twin
Ecosystem: Nokia
Private Network: 5G
John Deere has successfully implemented a private 5G network at its Davenport Works facility in Iowa, marking a significant milestone in the company’s Industry 4.0 journey. This manufacturing powerhouse, spanning 2.2 million square feet, produces heavy equipment including four-wheel drive loaders, articulated dump trucks, and road graders for the construction and forestry industries.
The company is transitioning from a predominantly wired environment (70% Ethernet, 30% Wi-Fi) to a wireless-first approach, with plans to implement 80% mobile connectivity, while retaining just 10% Wi-Fi and 10% Ethernet connections in the coming years. This shift represents a fundamental change in how the manufacturer approaches factory connectivity.
According to Jason Wallin, John Deere’s principal architect of foundational IT, the private 5G network dramatically reduces downtime during system upgrades or outages, cutting cycle times from weeks to mere hours. Previously, the company had to schedule skilled trades to run wires, coordinate factory outages, and recalibrate systems afterward—a time-consuming and disruptive process.
The Davenport Works facility serves as what John Deere calls their “lighthouse factory” – the first place they implement and test new technologies before rolling them out to other facilities both domestically and globally. This strategic approach ensures technologies are thoroughly vetted before broader deployment.
Chief Technology Officer Jahmy Hindman explained that the company is focusing its private 5G deployment strategy on its largest manufacturing facilities with the most complex operational processes. The implementation began after John Deere successfully bid on CBRS priority access licenses in 2020, targeting areas where most of its manufacturing footprint exists.
One of the primary motivations for adopting private 5G was the increasing density of IoT devices on the factory floor. Hindman noted that as the company implemented its Industry 4.0 strategy starting in 2020, they found themselves constantly installing new IoT devices that required running “miles of Ethernet cables” to place Wi-Fi access points throughout their facilities. Additionally, Wi-Fi saturation was causing network connectivity issues that were becoming problematic for operations.
The technical implementation has shown impressive results, with Wallin noting that just six radio units can replace approximately 300 Wi-Fi access points. Hindman expressed pleasant surprise at the coverage density, observing “generally better coverage” with “fewer dark spots in the factory.”
The private 5G network supports numerous applications throughout the facility. Parts bins now automatically signal when inventory runs low, eliminating the previous manual notification process that caused production delays. Bar-coded components can be tracked across the factory floor using 5G and RFID technologies.
Smart tools have also been integrated with the network, including 5G-connected torque wrenches – the most commonly used tool in the building. These intelligent wrenches display assembly instructions on a screen, confirm when bolts are correctly installed, and record critical torque data for quality control.
Looking to the future, the company currently maintains a digital twin of the Davenport Works facility, containing specifications for every part, tool, and production sequence. Hindman envisions combining position triangulation capabilities with this digital twin to automatically update the virtual model in real-time based on physical changes in the factory.
The company is also exploring augmented reality applications for the factory floor, considering options from Meta Platforms and Apple. While interested in the potential of 6G technology, Hindman indicated that John Deere won’t be an early adopter, preferring to wait until the functionality and toolset create sufficient value to justify the change.